Alvedia’s High Manufacturing Quality Standards
Pioneering Excellence in Immuno-Chromatography & Gel Test Technology.
At Alvedia, we pride ourselves on maintaining the highest manufacturing quality standards in the production of our immuno-chromatography technology.
Our entire manufacturing process is conducted in-house at our state-of-the-art facility in France, ensuring rigorous control and consistency at every stage. The production begins with the development of our proprietary monoclonal antibodies, followed by meticulous cell culture and antibody harvesting. Each batch undergoes comprehensive quality control, including flow cytometry analysis and specificity testing, to ensure robustness and accuracy. The antibodies are then dispensed onto strips and gels, with precise migration and stability tests conducted to verify performance under various conditions. A sophisticated traceability system tracks each reagent and component, ensuring complete transparency and recall capability. Finally, the products are assembled, packaged, and stored under optimal conditions, with ongoing long-term stability testing to guarantee reliability throughout their shelf life. This rigorous process ensures that every Alvedia product meets our exacting standards and delivers reliable results to our customers.
High Levels of Quality Assurance
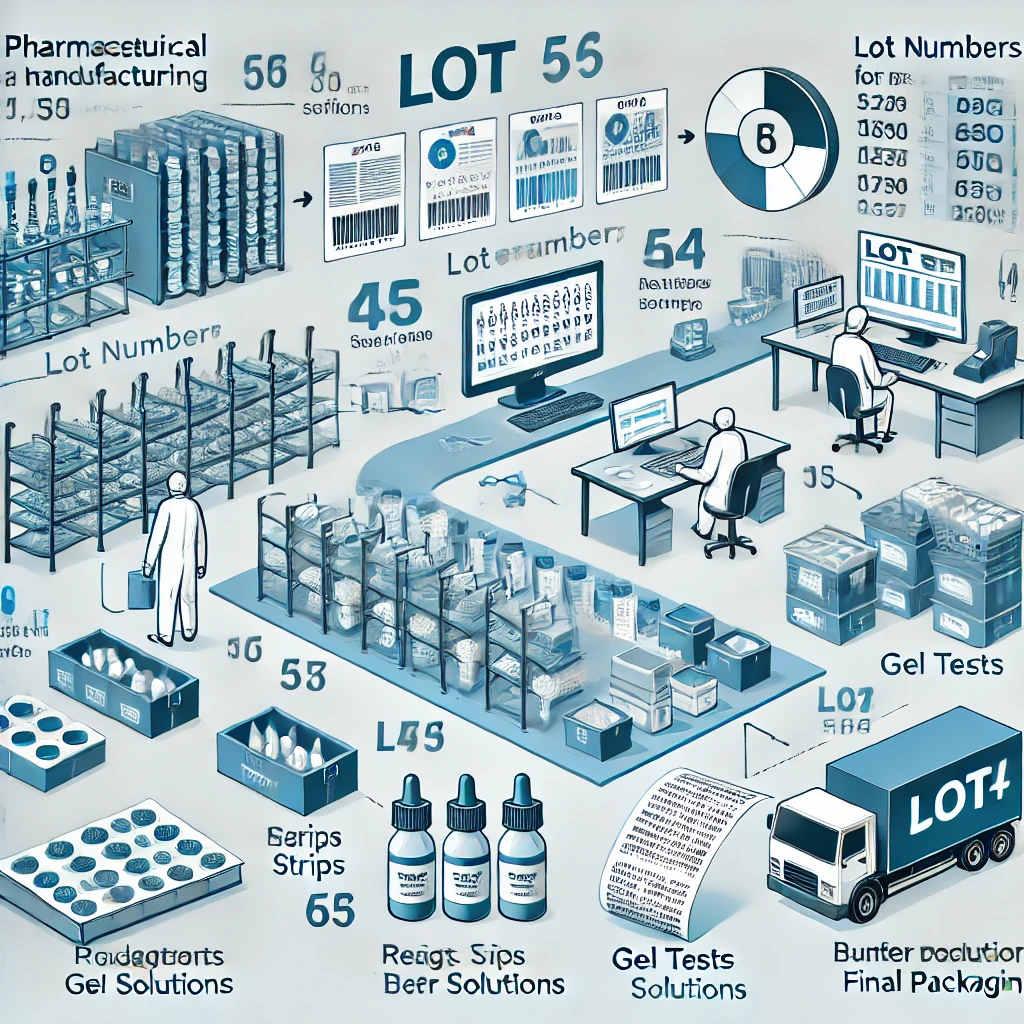
Comprehensive In-House Manufacturing
- All production processes are conducted at Alvedia’s state-of-the-art facility in France.
- This approach ensures rigorous oversight and quality control at every stage of production.
Proprietary Monoclonal Antibodies and cell Culture Production
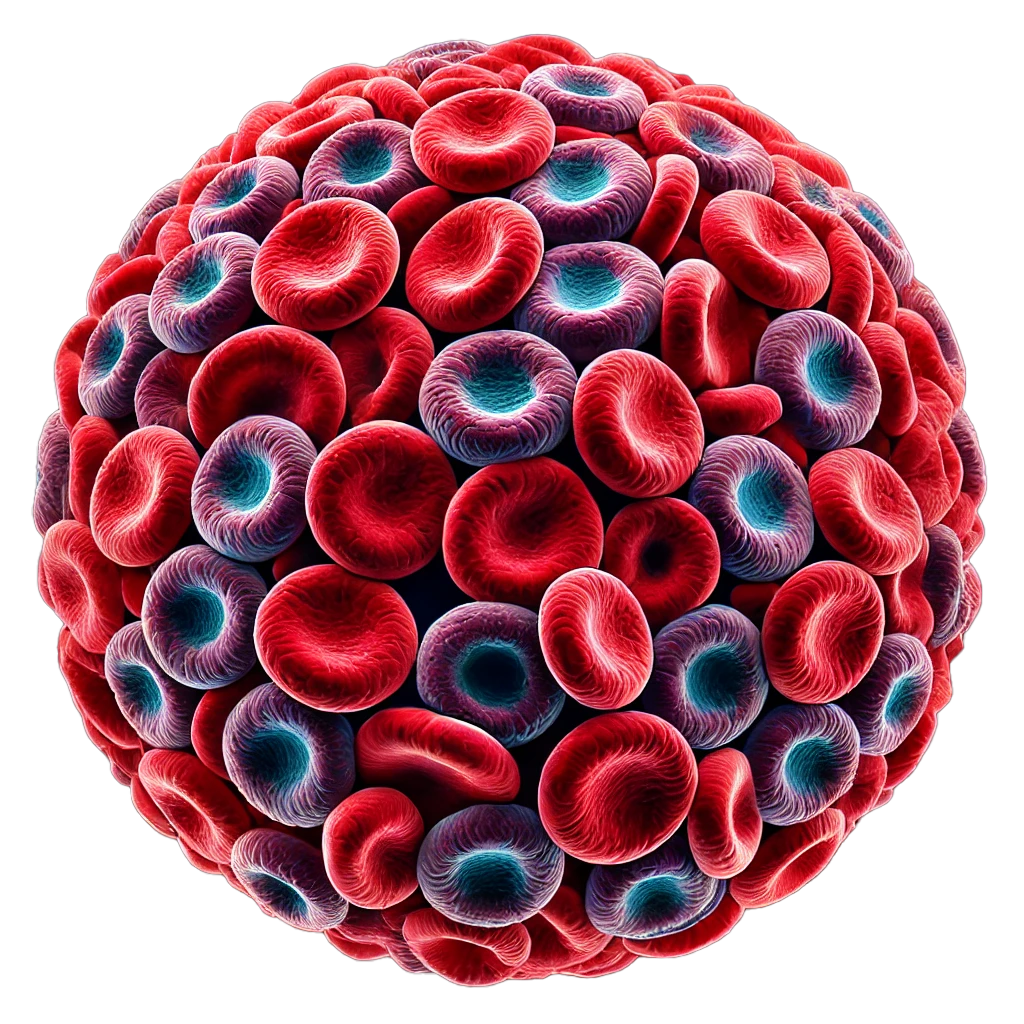
Exclusive Ownership of Clones
- All clones from monoclonal antibodies are proprietary to Alvedia.
- This exclusivity ensures unparalleled control over the quality and specificity of our products.
Scientific Advantage of DEA1 Antibody
- The DEA1 monoclonal antibody developed by Alvedia is the most specific antibody available.
- It effectively detects the full range of DEA1 antigens, providing precise and reliable results.
Innovative Monoclonal Antibody Development
- Each batch undergoes stringent quality control to verify specificity, stability, and robustness.
- Advanced flow cytometry is employed for precise specificity and calibration.
- Unique lot numbers are assigned for comprehensive traceability throughout the production lifecycle.
Dispensing Antibodies on Strips
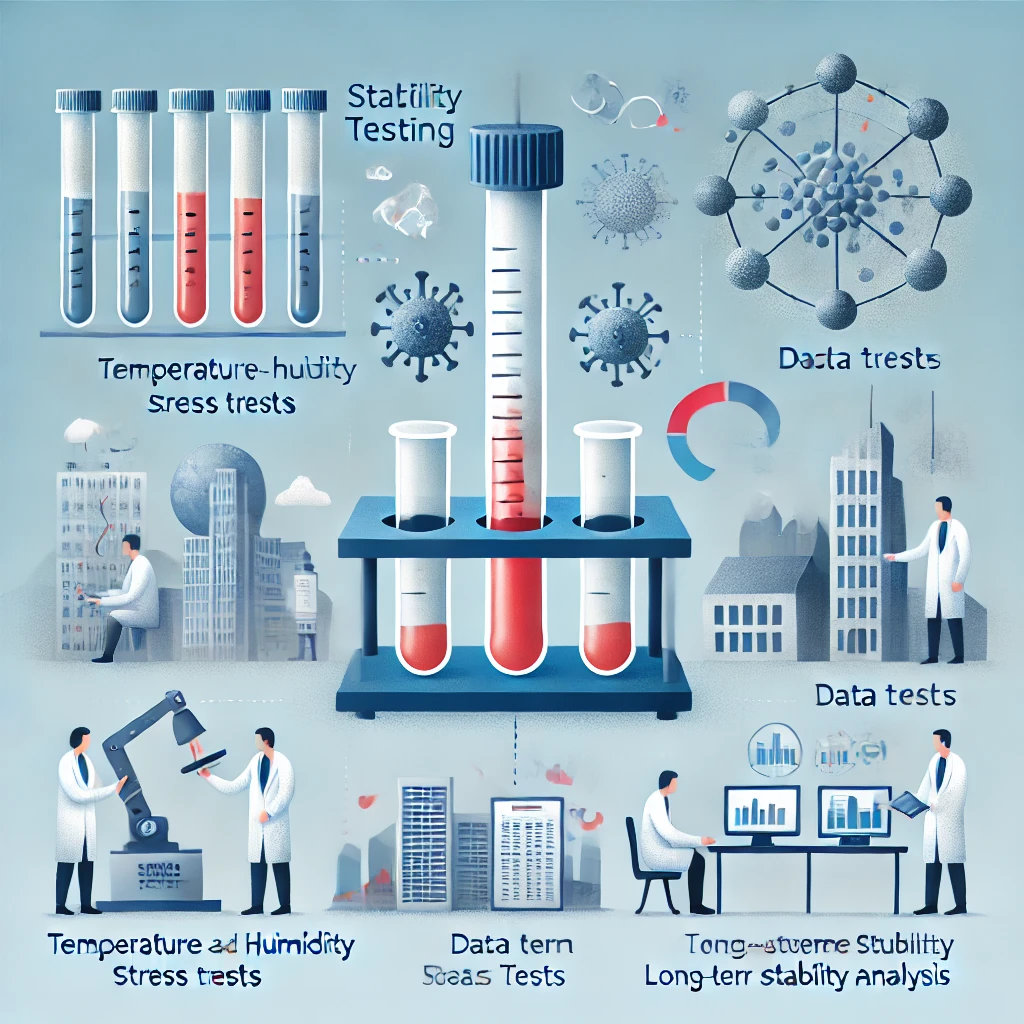
Precision Specificity Testing
- Each batch is validated using positive and negative controls to ensure accuracy.
- DEA1 line testing across multiple blood samples mitigates the risk of false positives and ensures weak positive reactions are identified.
Robustness and Migration Testing
- Flow cytometry analysis is utilized to correlate titer and intensity.
- Migration tests confirm that red blood cells traverse the strip correctly, with a standardized migration time of 2-5 minutes for strip technology.
Stability Testing Under Stress Conditions
- Products are subjected to controlled temperature and humidity stresses to confirm long-term antibody stability.
Advanced Traceability System
High-Level Traceability Protocols
- Detailed identification and documentation of all reagents and materials used.
- Distinct lot numbers are assigned for reagents, strips, gel tests, and buffer solutions, facilitating global recall capability if necessary.
Reception and Quality Control of Raw Materials
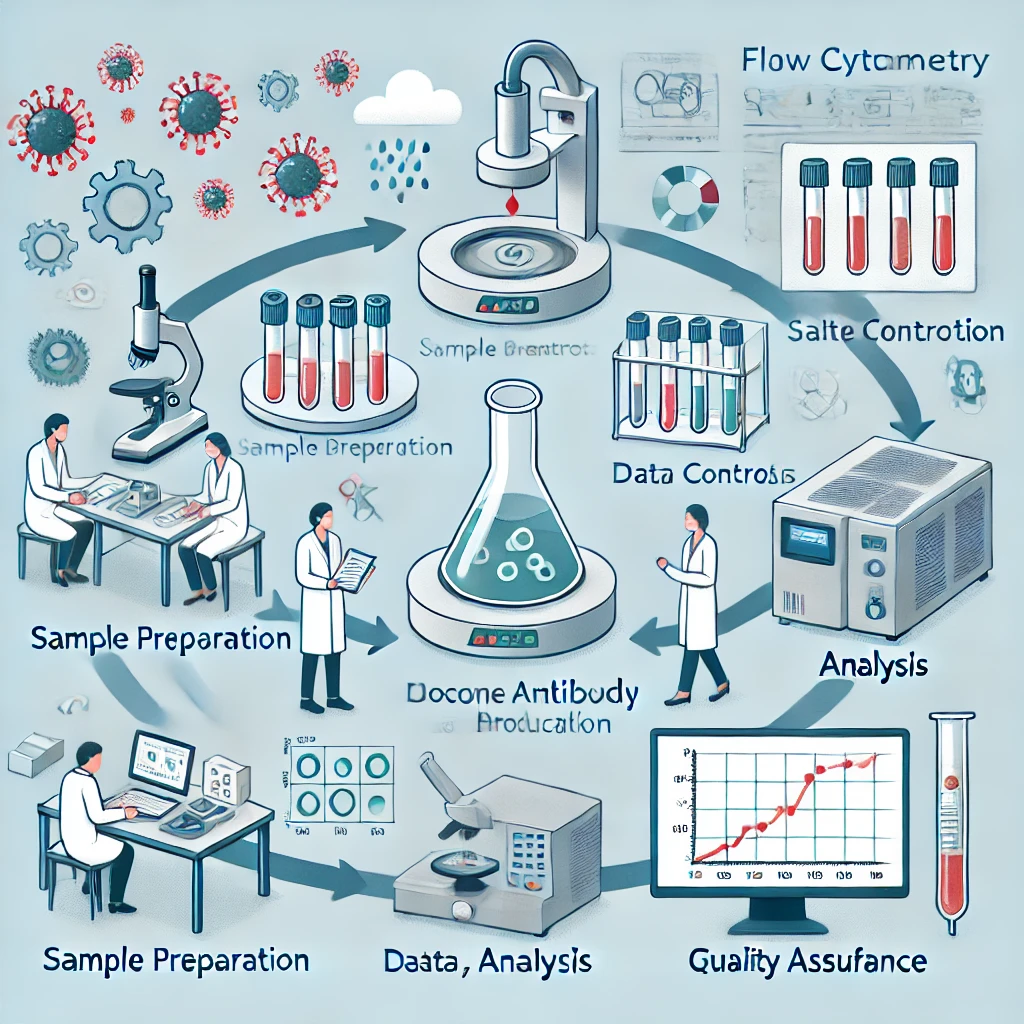
Rigorous Raw Material Verification
- Incoming raw materials undergo meticulous inspection and optimization processes to ensure they meet the highest standards for final packaging.
Controlled Product Assembly
Structured Assembly Procedures
- Each component is systematically verified and integrated into the final packaging, with an emphasis on maintaining stringent traceability throughout the process.
High-Standard Final Packaging Process
Optimized Storage Solutions
- Our advanced packaging techniques allow immuno-chromatography products to be stored at room temperature without compromising integrity or performance.
Long-Term Stability Assurance
Dedicated Stability Testing by Scientific Experts
- Comprehensive batch testing is conducted every 3 months to preemptively identify and address potential issues.
- Problematic lots can be efficiently recalled and replaced, ensuring continuous reliability
Final Quality Release
Issuance of Quality Assurance Certificates
- Each product undergoes final validation to ensure it meets our stringent quality standards before being released to the market.