High Standard Manufacturing
STEP 1 : CELL CULTURE PRODUCTION OF EACH MONOCLONAL ANTIBODY
Quality control of each batch to ensure the specificity, stability and robustness of each monoclonal antibody. Each batch will have a specific lot number that will be followed up during the entire production process. Some monoclonal antibodies are tested using flow cytometry analysis to ensure the best specificity and calibration between batches.
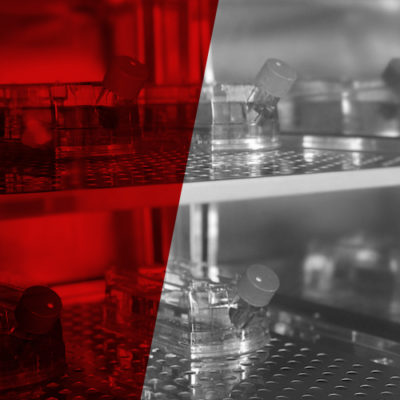
STEP 2 : DISPENSING MONOCLONAL ANTIBODIES ON THE STRIP
OUR PRODUCTION UNIT WILL ALWAYS START THE DISPENSE BY TESTING THE FIRST STRIPS TO ENSURE THE RELIABILITY OF THE TEST.
1. SPECIFICITY OF THE PRODUCT
For each batch, we test the specificity of the product with known positive and negative controls
Example for the Production of the Canine Blood Typing product:
Our scientific team will ask the production manager to give the first strips for testing purposes before launching the entire production.
We will test first the specificity: A DEA1 positive dog must show a line where the DEA1 monoclonal antibody line was placed.
A DEA 1 negative dog must have no line where the DEA1 monoclonal antibody line was placed. The line must stay negative in order to check that NO weak line (or faint line) will appear after drying and to avoid false positive result.
2. ROBUSTNESS OF THE PRODUCT
Using Flow cytometry analysis, we will ensure that the Intensity of the DEA1 line will correlate with the level of expression of the DEA1 antigen.
A low level of intensity must appear showing a weak line in front of DEA1 line, a high level of intensity must show a strong line in front of DEA1 line.
(For more specific explanation on Flow cytometry analysis technology, you can visit our page “Veterinary scientific research”)
Once passing these quality controls, (specificity and robustness) the entire production is launched with a unique batch number (LOT N° on the product label)
3. MIGRATION OF RED BLOOD CELLS
Our Immuno-chromatography technology is reliable using whole blood or packed red blood cells. We proceed to quality controls of the membrane in order to make sure that Red Blood cells will migrate correctly all along the strip. We calculate the time of migration from the bottom of the strip to the top and we accept a range between 2 minutes to 5 minutes.
4. STABILITY TESTING
At the end of the production process, several strips (beginning, middle and end of production) are going into stability testing. We “stress” the products by increasing the temperature and the humidity rate during several days. The antibodies must be stable all along this process to ensure a long term stability.
Once passing the stability testing the entire production is released for final packaging.
A total of 5% of our production is kept for long term stability at room temperature in both packaging (Aluminum foil and silica tubes)
This procedure also allows our scientific team to test each batch in case of a claim request (you can download the file “product claim form” on our website)
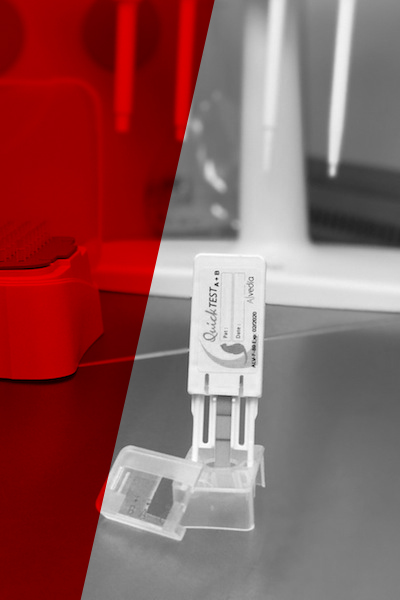
STEP 3 : TRACEABILITY SYSTEM (LOT NUMBERS)
Our traceability system is based on a high level of requirements. From the beginning to the end of the production, we are able to identify each reagent used and all relevant information we must know to follow our products during the entire shelf life of the product.
Each Test will have a specific lot number for the strip and another one for the buffer solution. In applying this policy, we are able to proceed to a lot recall at any time and all over the world. Our local distributors must keep a file with each lot that has been sold
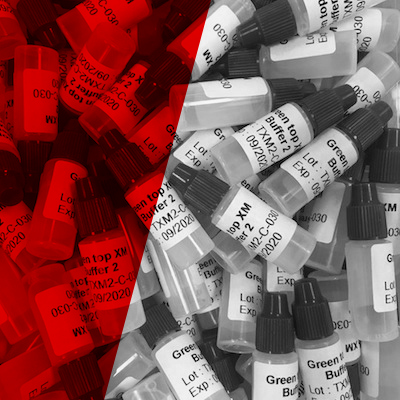
STEP 4 : LABELLING PROCESS
Labelling of each lot number is made in house to ensure the best traceability process. We control each step of this process to avoid any troubles.
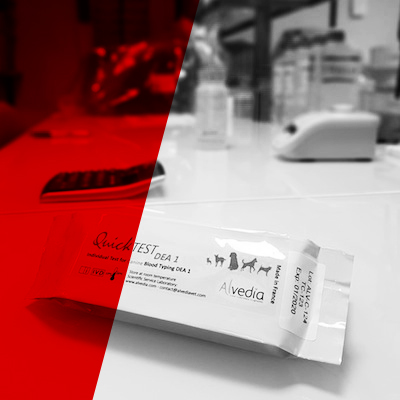
STEP 5 : RECEPTION OF THE RAW MATERIAL
Control process to check and optimise the use of raw material for the final packaging.
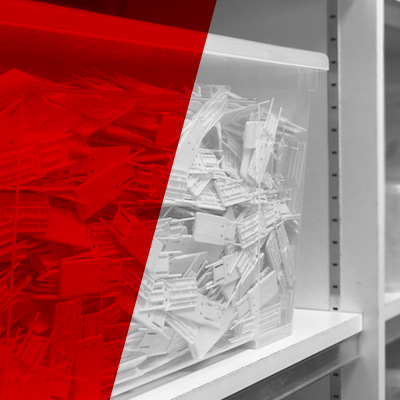
STEP 6 : PRODUCT ASSEMBLY
We follow a step by step procedure to ensure that all equipments are correctly included into the final packaging. We have initiated quality controls at each step of the production process.
One of the main purposes is focus on traceability procedure.
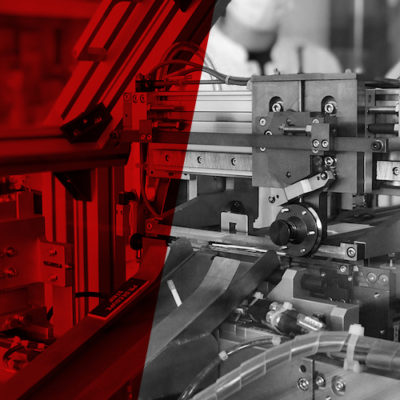
STEP 7 : FINAL PACKAGING PROCESS
All our Immuno-Chromatography products can be stored at room temperature thanks to our high quality packaging standards.
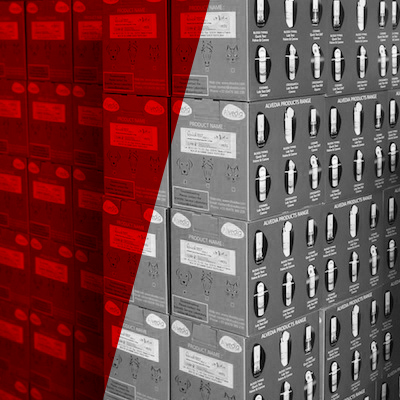
STEP 8 : LONG TERM STABILITY
Our scientific team is dedicated to providing a product that will be reliable during the entire product’s shelf life.
To anticipate potential result issues, our scientific team is testing ALL our batches that are currently available on the market EVERY 3 MONTHS.
If a problem occurs, we will be able to recall only the lot concerned and replace it by a new product.
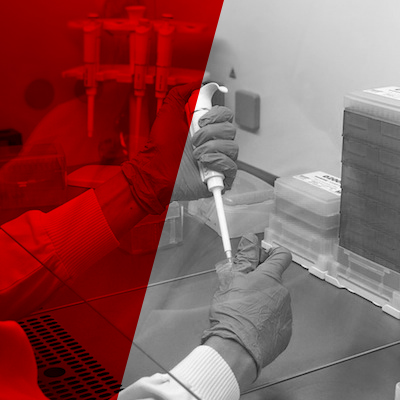
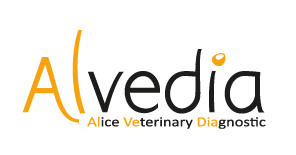
11-13 Rue des Aulnes,
69760 Limonest
+33 478 380 239
contact@alvedia.com